調査・研究
サービス概要
社会の物流ニーズを先取りする、という視点から調査を実施し、実現のための課題を明らかにします。
-
経済と貨物輸送の見通し
1974 年度の第1回調査開始。国内外における「経済」と「貨物輸送量」の動向を調査・分析するとともに、半年から1年程度先の短期的な動向について予測しています。
-
-
全国貨物純流動調査(物流センサス)
物流センサスは日本の国土交通省が 5 年ごとに実施している標本調査で、出荷側からの貨物の動きを調査している、日本で唯一のものです(国土交通省様委託業務)。
-
物流事情調査
新興国を中心に 30ヵ国以上の調査実績。新興国は制度や事業環境の変化が速く情報が陳腐化することなどから、必要に応じた国・地域、業種に絞って調査が可能です。
-
グローバルマーケットレポート
各国市場・物流制度・現地運用に精通したプロが貴社の海外展開を徹底支援。調査・分析・コンサルティングでグローバルビジネスを加速させます。
-
最先端技術動向
世界各地で行われている最新技術および物流関連の展示会に参加。また海外の物流関連研究機関とも情報交換を行っており、常に新しい情報を収集・分析しています。
-
物流施設立地評価
物流施設を構築する際の立地評価を行います。利便性、対象用地および周辺の作業環境や接道条件、周辺の物流施設の設置状況、関連統計資料等を多面的に分析します。
-
グリーン・ロジスティクス
排気ガス削減に向けた輸配送手段等に関する実態調査をはじめ、リサイクル輸送システムの構築や見直し、ご提案をします。
-
災害ロジスティクス
地方自治体様、物流事業者様に、災害発生時の物資供給計画を作成するための基礎調査、拠点配置・備蓄倉庫選定などのサービスを提供しています。
-
トライアル・実験
新しい物流技術のトライアル・実験を代行して請け負い、実証実験の企画と実施、結果の分析、結果報告、改善点のリストアップなどを行うサービスです。
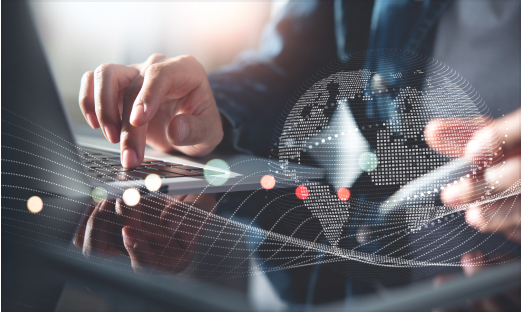
カスタム調査
NX総研では上記例に当てはまらない、貴社特有の事情やご要望によるカスタム調査もお受けしています。下記フォームよりお問い合わせ下さい。